PLASTIC INJECTION MOLD MAINTENANCE
The maintenance process of plastic injection molds is an extremely important factor, helping the machine operate smoothly, saving a significant amount of time and money. Proper maintenance of plastic injection molds is the basis for determining the quality of the mold for the next plastic injection cycles. In this article, we will learn more about the issue of plastic injection mold maintenance in production.
Some common errors when not maintaining plastic injection molds regularly.
Plastic injection molds can be used many times over a long period of time. However, using plastic injection molds for a long time will cause the mold to no longer ensure the original product quality. If plastic injection molds are not maintained carefully, serious degradation will occur. Common errors that are directly shown on the product include:
- Product surface has burn marks
- Product is brittle, easily cracked, broken
- Product is contaminated with oil
- Product is discolored
- Product has peeled plastic surface
- Product is deformed, concave or hollow
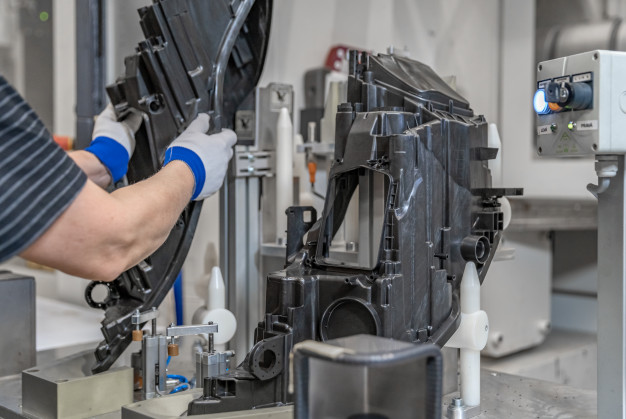
- Broken mold components
- The mold surface is oxidized, rusted
- Components are worn, deformed
How to fix common errors in plastic injection mold maintenance.
-
When the mold causes the product surface to burn, it should be remedied in the following direction: Add or arrange a ventilation system when entering the mold. On the other hand, it is necessary to pay attention to designing a reasonable thickness.
-
For brittle products that are prone to cracking and breaking: the cause may come from the nozzle, the channel or the nozzle, so it is necessary to redesign the plastic injection system appropriately to overcome this situation.
-
Peeling the surface of the plastic product is a serious error and the product will not meet the standards and will be discarded immediately after being pressed. The cause lies in the mold problem, it is necessary to smooth the sharp edges of the nozzle mouth and the channel.
-
Discolored products are often caused by molds, and can be fixed by redesigning the appropriate plastic channel system to reduce frictional heat that causes overheating.
-
Burrs are not serious errors, but they are the most common errors when plastic products are pressed out. However, although they are not serious errors, they are time-consuming and labor-intensive due to the need to remove excess plastic. To avoid this phenomenon on the product, when maintaining the mold, it is necessary to pay attention to the tightness and cleanliness of the mold parting surface.However, during the process of maintaining plastic injection molds, we need to observe carefully to see what errors the mold is having in order to make the right repair decision.
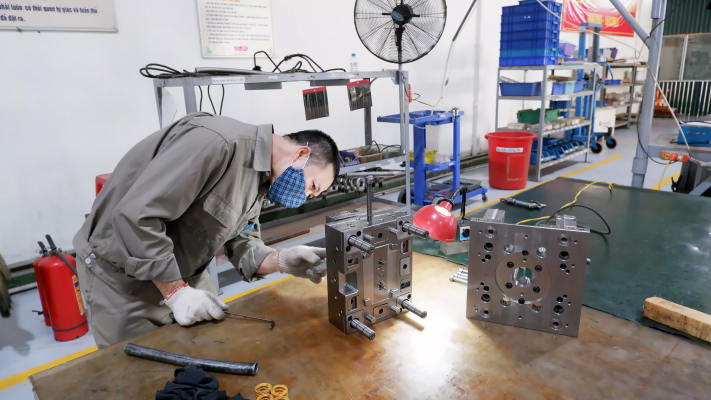
Items that need to be maintained for plastic injection molds
- Cleaning the mold parts will eliminate the situation of the product being oily
- Periodically check and maintain the air and gas vents to see if they are clogged, to fix them promptly.
- Check the cooling water line, prevent steam leakage
- Check the wear of components, especially for the mold parting positions
- Check the wear of the guide pins
- Clean thoroughly, remove plastic on the contact surface with the nozzle
- Treat the mold against rust that has not been used for a long time, maintain it before stopping use.
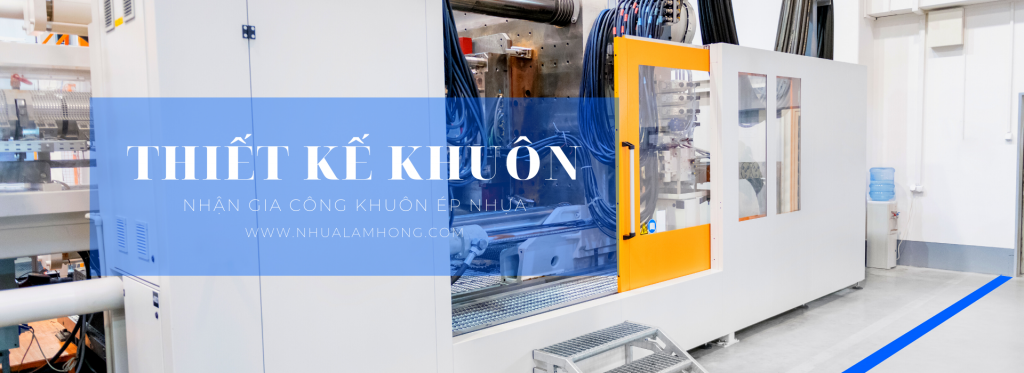
Customers who need to make plastic molds domestically and internationally, please contact us via the following information: